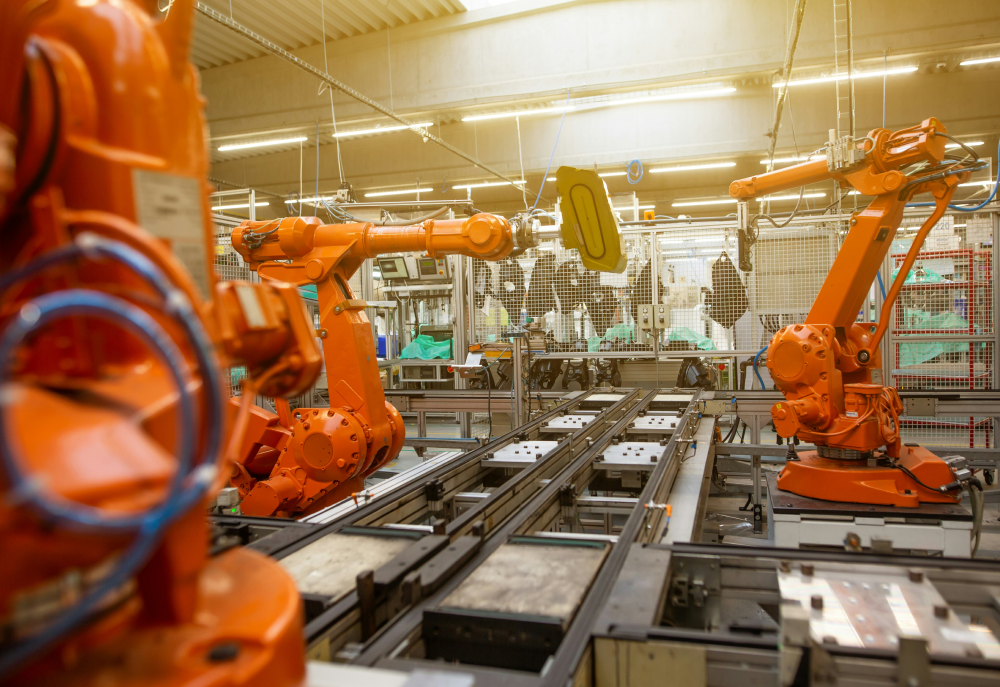
Digitalization Paves the Way for Green Production and Sustainability
In today’s industrial landscape, digitalization isn’t just a trend—it’s a revolution. As companies seek more sustainable and efficient operations, integrating digital technologies has become essential. This article explores how digitalization impacts green production and sustainability, highlighting the benefits, challenges, and future trends.
So, What Exactly is Green Production?
Green production means manufacturing products by minimizing environmental impacts, conserving energy and resources, and being economically viable and safe. It is not limited to just using renewable energy and reusing materials. It goes beyond that, involving process improvements, the adoption of smart technologies, and efficient resource management. Digitalization is crucial in this context, as it allows for monitoring and optimizing energy and material consumption, reducing waste, and increasing overall factory sustainability. In other words, "Green Digitalization" is essential for reducing environmental impact and enhancing both efficiency and profitability.
Companies adopt practices like renewable energy, recycling, and waste reduction, which not only protect the environment but also improve financial outcomes. Additionally, technologies such as the Industrial Internet of Things (IIoT) and real-time data analytics help monitor and optimize resource use, increasing efficiency and reducing waste—key examples of digitalization.
Benefits of Digitalization for Sustainability:
Increased Efficiency and Waste Reduction
One of the most significant benefits of digitalization in the industry is increased efficiency. By utilizing technologies like predictive maintenance, companies can prevent equipment failures and reduce downtime. This not only saves costs but also conserves resources by extending the lifespan of machinery.
Moreover, digital tools provide insights into energy consumption and resource usage, allowing companies to implement more sustainable practices. For example, production monitoring systems track energy usage and identify areas for improvement, leading to significant energy savings and reduced carbon footprints. In fact, digitalization of the shop floor can help reduce carbon emissions by 20%, according to the GeSI and Accenture report (2015).
Improved Design and Development of Sustainable Products
Digitalization also facilitates the design and development of sustainable products. Through digital twins and simulation technologies, manufacturers can model and test products virtually before beginning physical production. This reduces the need for prototypes, conserving materials and energy.
Additionally, real-time data analysis allows companies to assess the environmental impact of different materials and processes, guiding more sustainable choices. This level of insight is invaluable for companies committed to reducing their ecological footprint and aligns with the growing consumer demand for more sustainable products.
Challenges in Implementing Digital Solutions
High Initial Costs and Technical Barriers
Despite the numerous benefits, implementing digital solutions in the industry presents challenges. One of the main obstacles is the high initial investment required for digital infrastructure. Upgrading existing systems, acquiring new technologies, and training staff can be expensive and time-consuming.
Technical barriers also pose a challenge, as integrating new digital tools with existing systems can be complex, requiring specialized expertise. Additionally, concerns over data security and privacy can hinder the adoption of digital solutions, as companies must ensure their systems are protected against cyber threats.
Change Management and Workforce Adaptation
Another significant challenge is change management. The shift to digital operations requires a cultural change within the organization. Employees may resist new technologies, especially if they feel their jobs are at risk or if they are not adequately trained. To overcome this, companies can invest in training programs and foster a culture of continuous learning. By involving employees in the digital transformation process and demonstrating the benefits of new technologies, companies can facilitate the transition and ensure successful implementation.
Looking to the Future: Trends in Digitalization and Sustainability
The future of production lies in smart factories that use IIoT, AI, and machine learning in fully automated and efficient environments. With minimal human intervention, these factories optimize production and resource use, enabling real-time decision-making and predictive maintenance. Moreover, the circular economy is emerging, aiming to reduce waste and maximize resource use. Digital technologies facilitate material management, promoting recycling and reuse. Real-time data helps design products that are more durable and easier to repair or recycle.
Platforms like proGrow provide the necessary support to follow these trends, offering the tools and insights crucial to thriving in the digital age. The ability to analyze real-time data is vital for maintaining market competitiveness and making your factory greener, and proGrow is ready to assist your organization in this process.
Join us in leading the future of a more sustainable industry through digital transformation!
Is your production efficiency a mystery?
Use our OEE Calculator and gain access to real data from your industrial machines to optimize your factory!
More articles
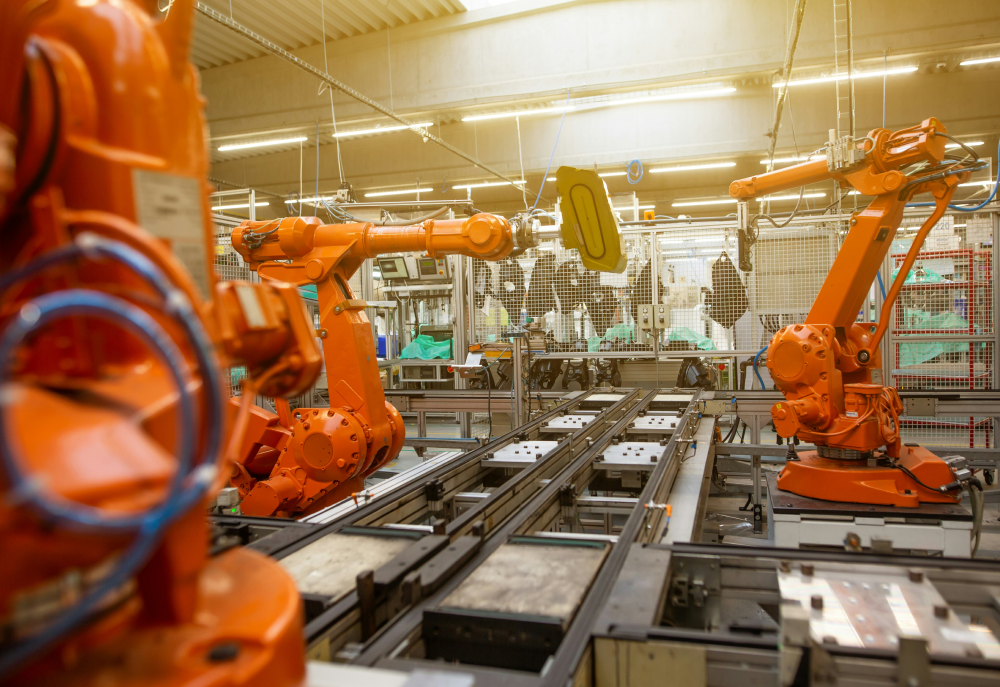
Digitalization Paves the Way for Green Production and Sustainability
Discover How to Make Your Factory Greener Through Digitalization!