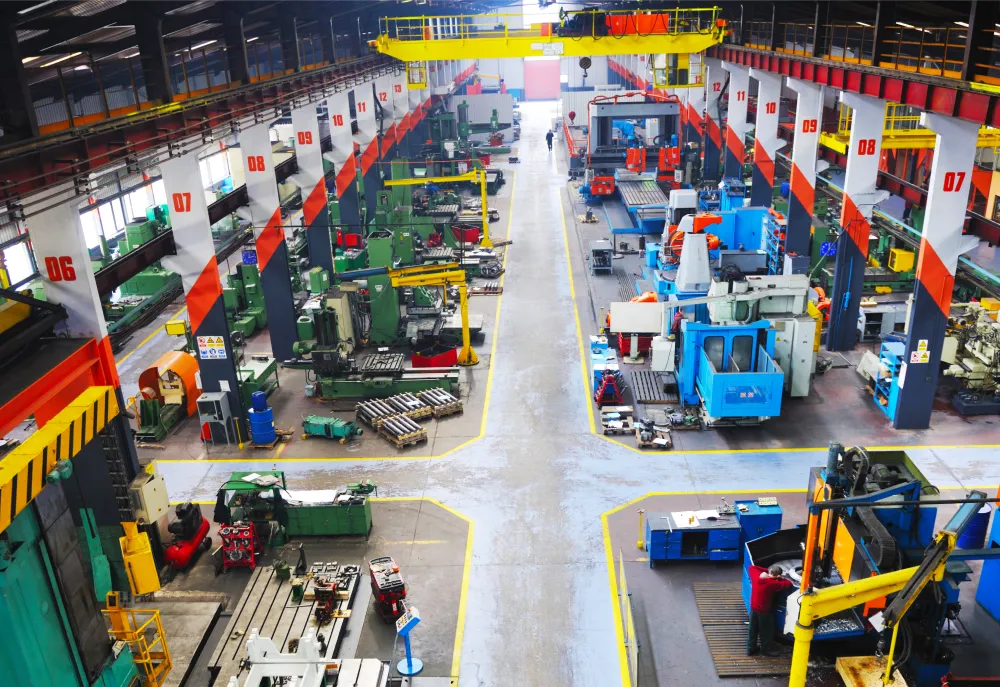
Manufacturing Data: Why Contextualization is the Missing Key
Nowadays, factories are starting to collect large amounts of data from sensors, machines, and other systems to optimize processes and improve production. However, raw data alone is not enough. This is where an important component comes in: Data Contextualization.
What is Data Contextualization?
Contextualization is the process of analyzing data within its informational context to gain insights and make informed decisions. In the industry, contextualization involves gathering data from multiple sources, correlating it, and analyzing it to gain knowledge about production processes. By analyzing data in context, operations can identify patterns, trends, and anomalies that may not be apparent in raw data. Contextualization also helps pinpoint root causes of problems and implement corrective actions.
Benefits and How Contextualization Works
Contextualization is a catalyst for transforming raw data into actionable knowledge. Here are some practical ways to apply it and the benefits it can bring:
- Identifying patterns and trends: With contextual analysis, it is possible to uncover patterns in data that indicate opportunities to improve production efficiency or predict problems before they occur.
- Automation and data integration: Systems like ERP, planning tools, or MRP can be used to add context manually or automatically. For example, sending manufacturing orders, production specifications, and operator information directly to equipment.
- Anomaly diagnosis: By correlating data such as downtime, types of rejections, and triggered alarms, it is possible to detect performance deviations and act quickly to correct them.
- Root cause analysis and informed decision-making: Access to detailed context facilitates root cause analysis, allowing for more precise and effective decisions, such as operator training or process adjustments.
A Practical Example of Contextualization
Imagine a situation where a machine has more downtime than similar machines. How can contextualization help find the root cause?
With contextual analysis, you can answer questions like:
- When did the downtimes happen?
- When did they start?
- How does the downtime compare to other machines?
- What products were being produced?
- Who might know what happened?
- What types of stoppages were reported?
- What alarms were triggered at that time?
With these answers, you might conclude, for example, that operators on a specific shift did not receive proper training to set up the machine correctly, resulting in longer downtimes. The solution would be a corrective action to train the team and reduce downtime.
Without contextualization, decisions may be based on incomplete or inaccurate data, leading to costly errors and reduced productivity. Contextualized data, on the other hand, speeds up problem-solving and makes operations much more efficient.
Ready to Transform Data into Knowledge?
At proGrow, we help companies contextualize their production data to maximize efficiency and drive results. Discover how we can help your operation reach the next level!
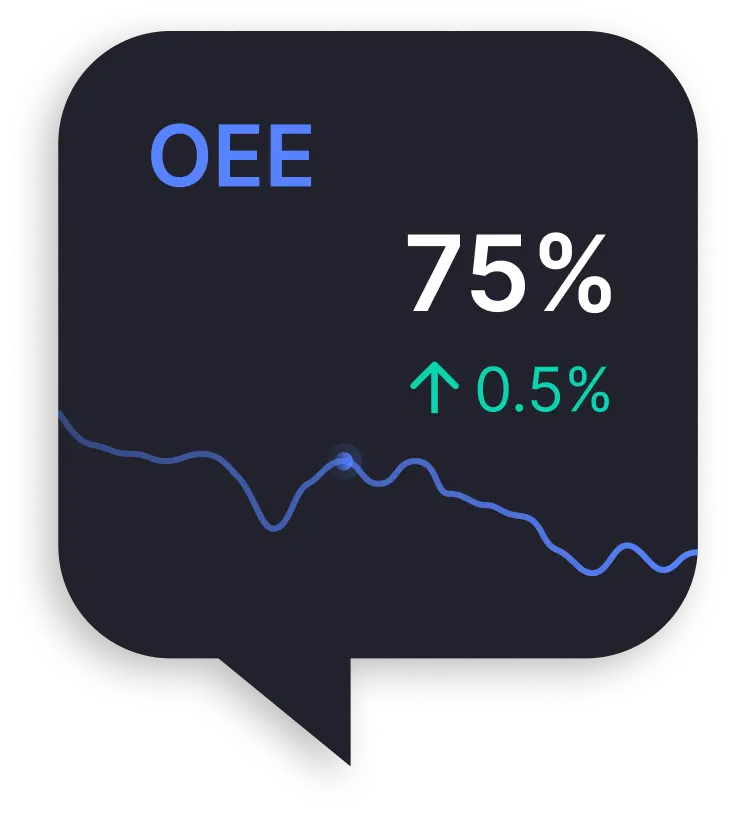
More articles
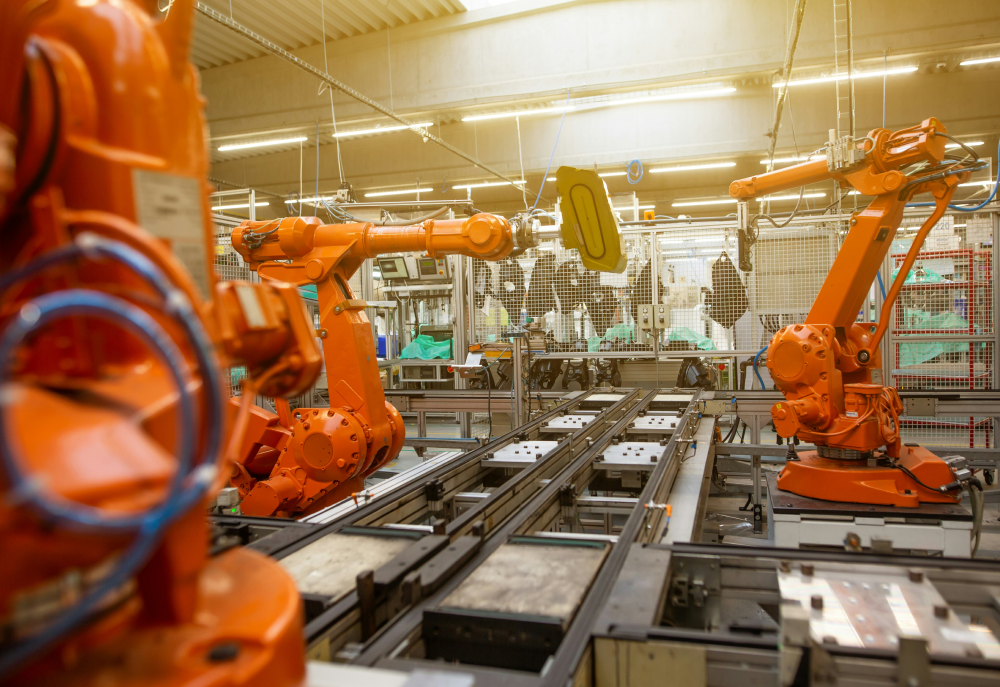
Digitalization Paves the Way for Green Production and Sustainability
Discover How to Make Your Factory Greener Through Digitalization!