%201.png)
Smart Manufacturing: The key to more efficient production
Data is revolutionizing the industry, enabling automation and smarter decision-making, a process known as Industry 4.0. However, factories still face significant challenges on this journey, such as attracting and retaining employees, supply chain disruptions, new regulations, cybersecurity threats, and integrating new technologies. Despite these hurdles, there is reason for optimism as the rapid adoption of technologies like IoT, cloud computing, and automation brings numerous advantages, despite initial costs. Data is essential for overcoming challenges, reducing costs, and improving productivity.
What is Smart Manufacturing?
Smart manufacturing is the strategic application of data and digital technologies to optimize production processes, aiming for seamless integration between the physical and digital worlds. It operates in three key stages:
- Capture: Smart manufacturing provides real-time visibility into industrial processes, collecting and integrating data from various sources such as IoT sensors, management systems, and production equipment. This comprehensive data collection forms the foundation for understanding operational performance.
- Understand: Once captured, the data is analyzed to generate meaningful insights. This involves identifying causes of disruptions, monitoring key performance indicators (KPIs), and detecting patterns and anomalies that might impact production. Analyses should be accessible and understandable for all stakeholders, regardless of their technical expertise.
- Act: Understanding the data is just the beginning. The real value of smart manufacturing lies in the ability to transform insights into concrete actions. This can include immediate process adjustments, predictive maintenance, resource optimization, and continuous improvement. The effectiveness of these actions depends on the quality of the data and analyses, ensuring decisions are based on accurate and relevant information.
Benefits of Smart Manufacturing
The benefits of adopting smart manufacturing are vast and transformative. First, resource optimization reaches new levels of efficiency. With detailed data on machine performance and resource usage, manufacturers can reduce waste, minimize downtime, and ensure every asset is used to its fullest potential. Predictive maintenance, enabled by real-time data, avoids costly breakdowns by scheduling repairs precisely when needed.
Additionally, financial and process planning becomes significantly more precise. Analyzing historical and current data allows manufacturers to forecast trends, allocate resources efficiently, and plan budgets with greater accuracy. This data-driven approach not only enhances financial control but also strengthens strategic decision-making.
The impact of smart manufacturing is undeniable. A Deloitte study found that smart factories deliver substantial improvements in costs, productivity, quality, safety, and revenue growth. They achieve this by combining technologies like the Industrial Internet of Things (IIoT), cloud computing, robotic process automation (RPA), artificial intelligence (AI), machine learning, vision systems, and augmented and virtual reality.
The same study also revealed that in the United States, 86% of manufacturers believe smart factories will be the main driver of competitiveness by 2025, and 83% predict these factories will radically transform how products are made.
Challenges and Considerations
While the benefits are enticing, implementing smart manufacturing also presents challenges. A significant hurdle is integrating new technologies with existing systems. Many manufacturers operate with equipment that may not be compatible with some modern IIoT solutions. Overcoming this challenge requires careful planning and often substantial investment.
Another challenge is ensuring data security. Increased connectivity brings a heightened risk of cyber threats. Manufacturers must implement robust security measures to protect sensitive information and maintain operational integrity. Investing in reliable cybersecurity protocols is essential to defend against potential attacks.
Future Trends in Smart Manufacturing
Looking ahead, several trends are shaping the evolution of smart manufacturing. Enhanced AI and machine learning capabilities are expected to revolutionize predictive maintenance and quality management. As algorithms become more sophisticated, they will offer even more precise predictions and insights.
Furthermore, the growth of edge computing will improve real-time data processing. By analyzing data closer to the source, manufacturers can achieve faster response times and reduce latency. This advancement will significantly boost production responsiveness and operational agility.
At proGrow, we understand the critical role smart manufacturing plays in modern industrial success. Our platform leverages advanced IIoT, production monitoring, and real-time data analysis to empower manufacturers with actionable insights. With proGrow, you can achieve unparalleled visibility on the factory floor, optimize resources, and enhance quality management. Our solution is designed to integrate seamlessly with your existing systems, overcoming common challenges like equipment compatibility and data security.
Ready to transform your production process?
Contact us today to get started!
Is your production efficiency a mystery?
Use our OEE Calculator and gain access to real data from your industrial machines to optimize your factory!
More articles
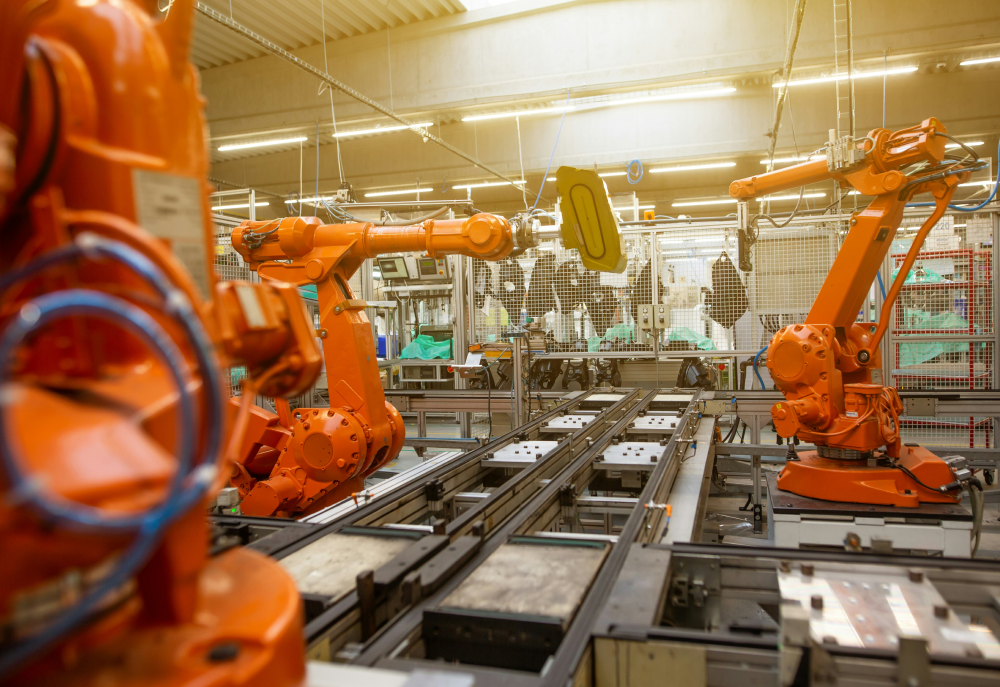
Digitalization Paves the Way for Green Production and Sustainability
Discover How to Make Your Factory Greener Through Digitalization!