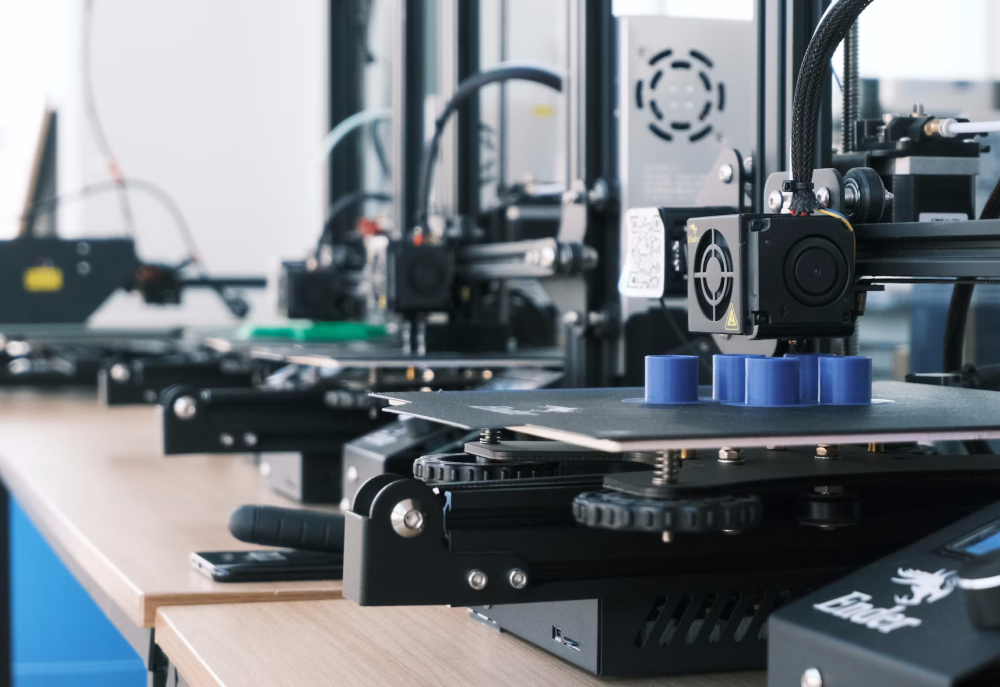
Digital Twin in Production: What You Need to Know
What is a Digital Twin?
A Digital Twin is a virtual representation of an object, equipment, or system that accurately reflects a physical object. This digital model tracks the entire lifecycle of the object and is continuously updated with real-time data, using simulations, machine learning, and reasoning to support decision-making. The growing prevalence of IoT devices and sensors provides a wealth of real-time data that can be integrated into the solution. This connectivity enables accurate and dynamic representations of physical entities.
How Does a Digital Twin Work?
The object being studied is equipped with sensors that capture information about key areas of its operation. These sensors generate data on various aspects of the physical object’s performance, such as energy production and temperature. Finally, the data is processed and applied to the digital model.
With this data in hand, the digital model can be used to run simulations, analyze performance issues, and suggest improvements. The goal is to obtain valuable insights that can be used to enhance the original physical object.
Industries often use Digital Twins to remotely monitor and control production facilities, enabling real-time visibility into operations, facilitating quick decision-making, and allowing responses to changing conditions.
Thus, the use of Digital Twins helps reduce equipment downtime and increase production. Through constant monitoring and detailed analysis, it is possible to optimize processes and improve operational efficiency, from the assembly line to product lifecycle management.
Types of Digital Twins
Depending on the level of product detail, there can be several types of Digital Twins. The main difference between these twins is their area of application, with different types often coexisting within a single system or process.
- Component Twins: The basic unit of a Digital Twin, representing the smallest example of a functional component.
- Asset Twins: Created when two or more components work together. They allow for studying the interaction of these components, generating performance data that can be turned into actionable insights.
- System or Unit Twins: At this level, it becomes possible to see how different assets combine to form a complete functional system.
- Process Twins: Reveal how systems work together to create an entire production facility. They help determine timing schemes that influence overall efficiency.
Advantages of Digital Twins
Improvement in R&D
Digital Twins facilitate research and product design more efficiently by generating large amounts of data on potential outcomes. These data can provide valuable insights that help companies make necessary product modifications before beginning production.
Increased Efficiency
After the start of production, Digital Twins continue to monitor systems with the goal of achieving maximum efficiency throughout the entire production process.
End of Product Life
Digital Twins also help manufacturers decide what to do with products that reach the end of their lifecycle. This virtual representation allows them to determine which materials from the product can be, for example, recycled or repurposed, which in turn reduces costs and makes production more sustainable.
Disadvantages of Digital Twins
Higher Complexity Than Expected
Although Digital Twins may seem simple, many companies find their implementation more complicated than expected. This is especially true in organizations with existing IT infrastructures, which may need to be updated before they can create digital replicas effectively and economically.
Poor Data Quality
A Digital Twin requires the right data to function. A lack of data or poor data quality can limit the use of Digital Twin technology or make it completely unfeasible.
Need for Customization
Business leaders need to tailor the Digital Twin to their organization’s specific needs and goals, as there is no one-size-fits-all solution. This process requires more time and effort, resulting in additional costs.
High Costs
During the implementation process, companies may find that Digital Twins are more expensive than expected. The costs involved in creating and effectively using this technology can delay the return on investment (ROI) for many organizations. While the technology has great potential, it may still take time to bring financial benefits to many companies.
Is it the Right Solution for You?
Digital Twins can be an attractive solution for large companies that handle critical product development processes and have significant resources, offering advanced simulations and detailed analyses. However, for many companies, opting for simpler and more agile monitoring solutions, such as proGrow, may be the key to success in digitalization.
With quick implementation, low cost, and integration with any machine, proGrow offers valuable real-time insights without the complexity and high investment of Digital Twins.
Let proGrow guide you on this digital transformation journey.
Ready to take your manufacturing processes to the next level?
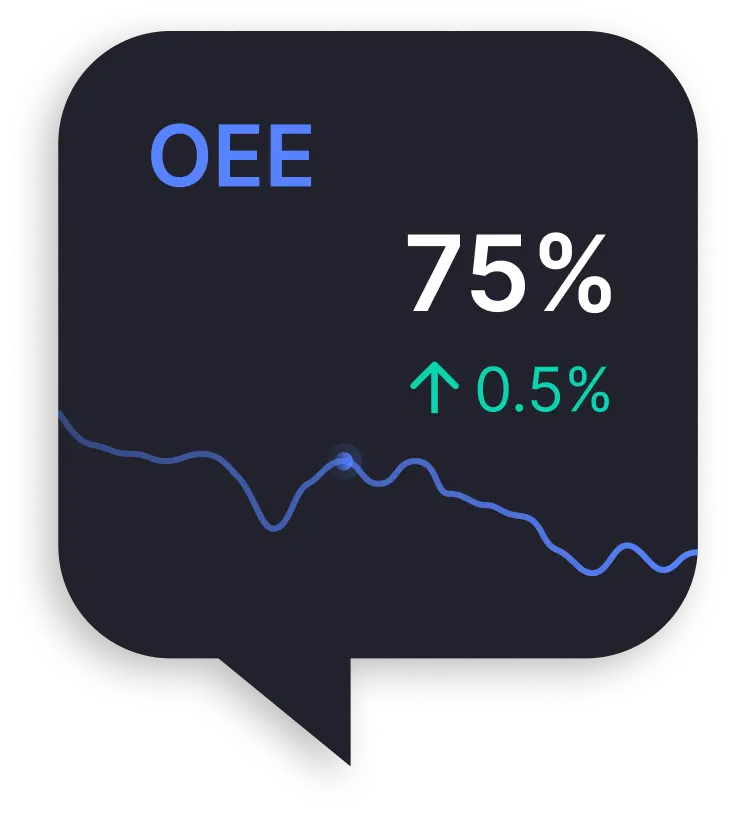
More articles
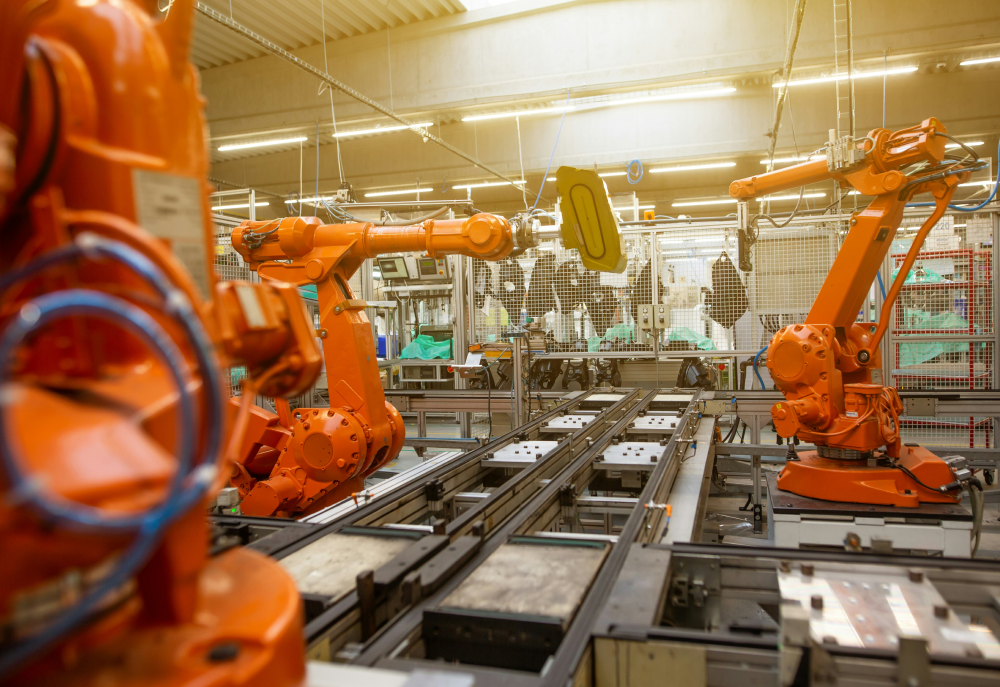
Digitalization Paves the Way for Green Production and Sustainability
Discover How to Make Your Factory Greener Through Digitalization!