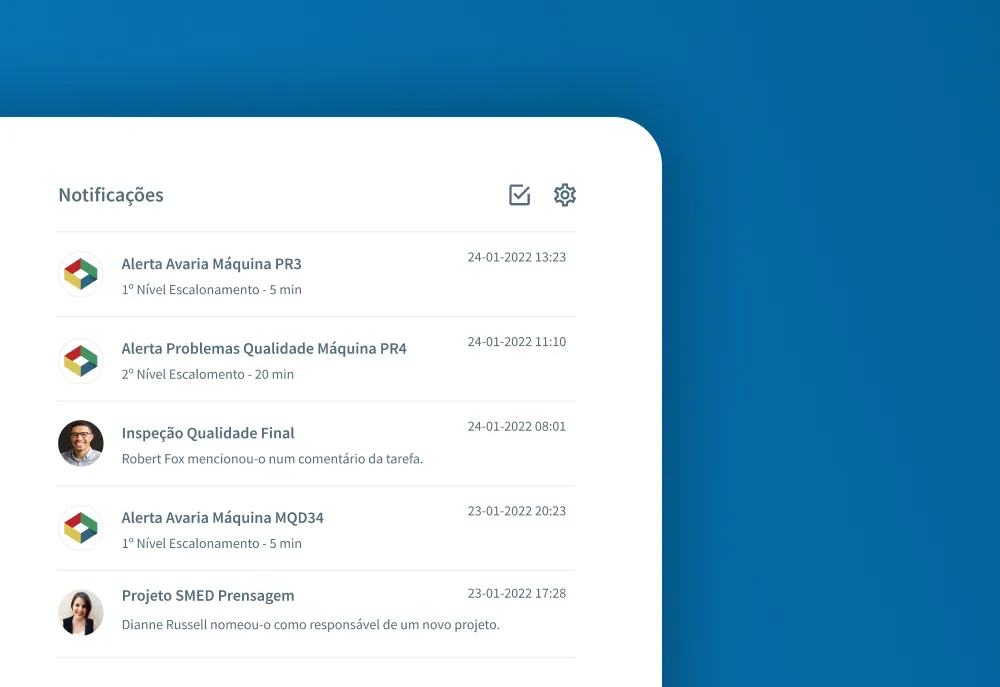
How having a digital alarm and escalation process can help operations
Connecting equipments and people also allows automating information flows. Having an alarm process and escalation of deviations allows you to notify the right person anywhere and in real time.
One of the main benefits of an alarm and escalation digital process is that it allows a timely and effective response to issues that may impact production or operations. For example, if a machine or piece of equipment begins to experience a malfunction, the alarm and escalation process can automatically detect the problem and notify the appropriate personnel, who can then take action to correct the issue and minimize downtime.
Another benefit of an alarm and escalation digital process is that it can provide valuable data and insights into the performance of operations. By tracking and analyzing data on key KPIs, such as energy consumption and production rate, managers can identify patterns and trends that can inform decision-making and process improvements.
Additionally, this functionality can also help improve security and compliance in operations. By automatically detecting potential safety risks or breaches of regulatory requirements, this real-time information can help protect workers and reduce the risk of breaching compliance in a manufacturing process.
How to have alarmistics and define escalation with proGrow
proGrow allows the definition of alerts of various types, such as changes in the state of the equipment, a break in an indicator result in relation to a reference value or change of a process control value outside the parameters. It is possible to configure which different response levels are required and who are the users who will receive each alert level. This allows a problem to be automatically escalated, notifying users on the platform progressively depending on the severity of the situation.
Additional information in the alert message: contextualization is everything!
In addition to the basic information of which alert was activated and at which escalation level it is, it is possible to customize the notification with some more useful information, such as a stoppage reason or the ongoing manufacturing order on the equipment.
Where do you want to receive notifications?
You can define where you receive the alert notification. Directly on the platform? By email? Or through an integration with an SMS service? It's your choice!
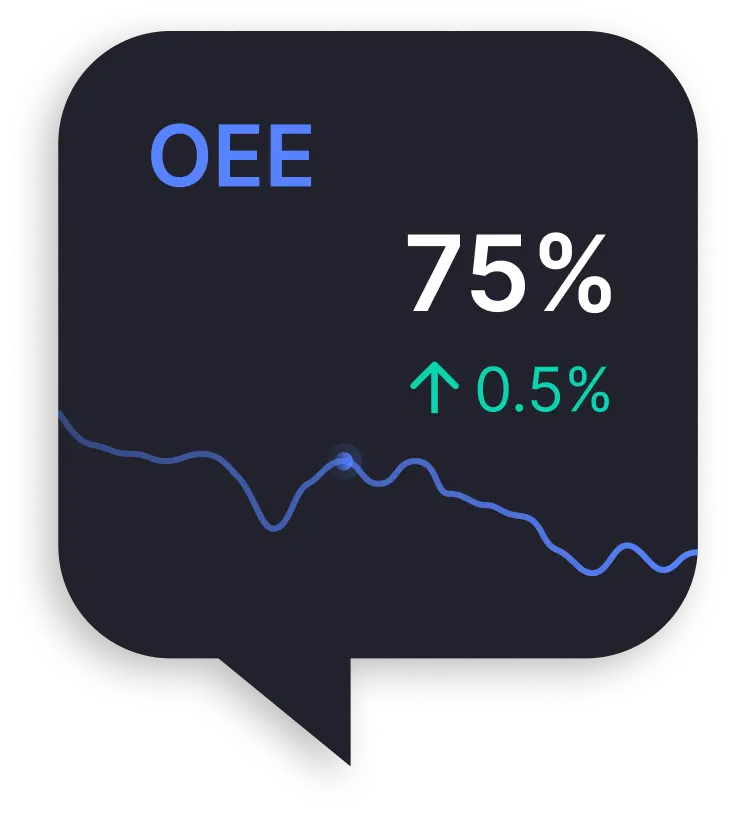
More articles
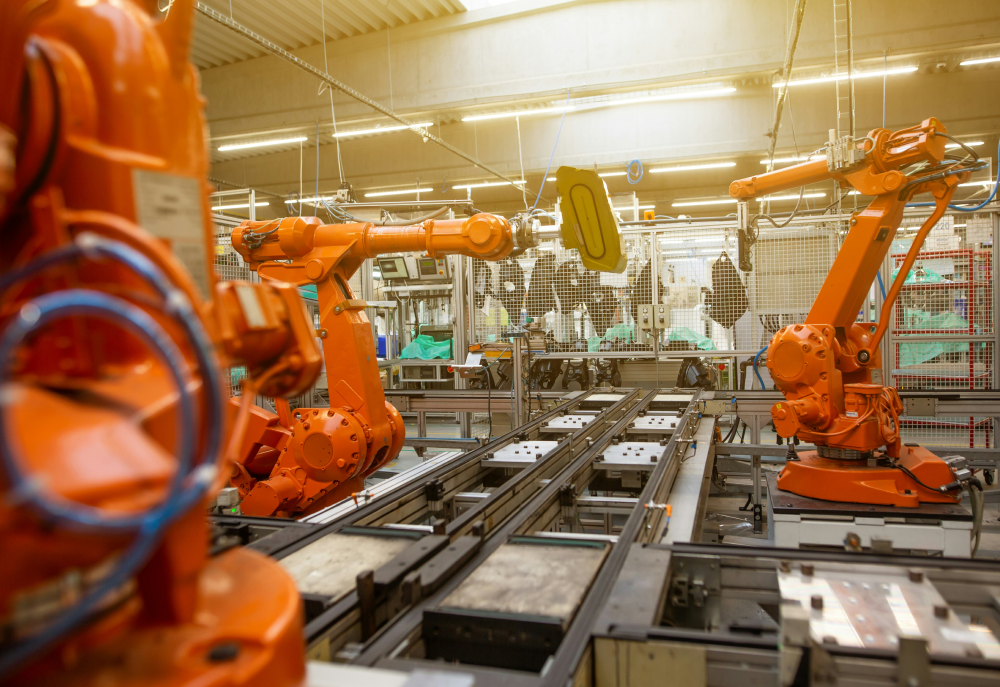
Digitalization Paves the Way for Green Production and Sustainability
Discover How to Make Your Factory Greener Through Digitalization!